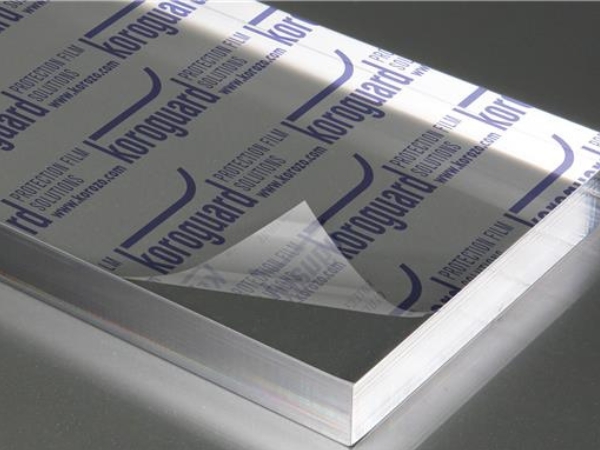
16/04/25
In the vast world of manufacturing and product packaging, few materials are as quietly essential yet often overlooked as surface protection films (SPF).
These thin, often transparent layers are critical in preserving the aesthetic and functional integrity of a wide range of products, from stainless steel panels and glass to electronics, automotive components, and household appliances. They stop scratches, prevent abrasions, and minimise contamination during manufacturing, transport, and installation. At the same time, they help to maintain the visual integrity of high-value surfaces like painted panels, brushed metals, and touchscreens. As such, despite their often fleeting presence, surface protection films play a pivotal role in maintaining quality throughout the supply chain.
This is evidenced by market statistics that anticipate the global market for SPF to grow steadily, with a compound annual growth rate (CAGR) of around 4.6%* from 2024 to 2034. This growth is driven by increasing demand in sectors like construction, automotive, and electronics.
Supply chain success
With SPF fundamentally being supply chain packaging and used to ensure protection during manufacturing and distribution, it’s likely that consumers rarely, if ever engage with these films.
That’s not to say consumers don’t benefit. On the contrary, big ticket items (cars, kitchens, televisions) are kept pristine and at their highest value because of SPF. A direct benefit for retailers and manufacturers is enhanced customer satisfaction and loyalty.
SPF also helps to promote operational efficiency within the supply chain, with products arriving in ready-to-install or ready-to-sell condition. By reducing the risk of damage, SPF help lower warranty claims and reduce the labour costs associated with repairs, fixes, and patches to damaged surfaces.
To advance the market position of SPF, innovations in film technology are leading to the development of films with enhanced properties such as improved resistance to chemicals, UV light, and high temperatures. These advancements are expanding the application range of these films into more demanding industries.
KoroGuard SPF is already suited to a wide range of applications and surfaces. In-house co-extrusion technology is used to manufacture protective films that are applied free of wrinkles and air bubbles to PET, PP, PETG, PMMA, ABS, High Gloss, SAN, PS, PC, HIPS, Glass, Metal, Semi Gloss, and Lacquered surfaces. Koroguard SPF can be provided in both adhesive and non-adhesive formats, with guaranteed residue-free removal. It can also be thermoformed and shaped directly to the product.
Sustainability matters
Sustainability is becoming increasingly important when it comes to SPF. These films have often flown under the radar in sustainability discussions, ending up as non-recyclable waste and rarely factored into environmental accountability.
The emergence and expansion of Extended Producer Responsibility (EPR) legislation is rapidly changing this as it is forcing the entire value chain – from the manufacturers to the users – to rethink the role and life cycle of every material used.
As already noted, SPF are often forgotten about in environmental assessments because they are temporary. Once their job is done, they’re discarded and usually end up as single-use plastic waste, with little thought given to their fate. Under EPR, such an ‘out of sight, out of mind’ mentality is no longer viable.
Whether for construction, automotive, electronics, or manufacturing applications, users of SPF must be aware of some significant developments:
Accountability for disposal
If importing or using surface protection films in a recovered by an EPR scheme, you will be responsible for the waste those films generate. This means tracking quantities, ensuring proper disposal, and in some cases, paying fees or contributing to recycling schemes.
Need for traceability
EPR frameworks often require full traceability. You must know where your protective films came from, what they’re made of, and where they go after use.
It’s time to stop thinking of protective films as ‘throwaway’ items and start treating them as a valuable part of the product value chain.
Contact us today to find out how our surface protection films are evolving and how we can help you with your surface protection and sustainability goals
*Future Market Insights, Surface Protection Film Market Outlook for 2024 to 2034
https://www.futuremarketinsights.com/reports/surface-protection-films-market